Turbo Assembly Checklist
When installing a new / different / used turbo unit, a few things are important to consider. If the old turbo has broken, you must first know why this has happened. Otherwise, the risk is high that the same thing will happen with the new turbo.Här går vi igenom hur du slipper problem
- Before assembly
- Mounting
- Start-up
- Troubleshooting
- Common causes of turbo failure
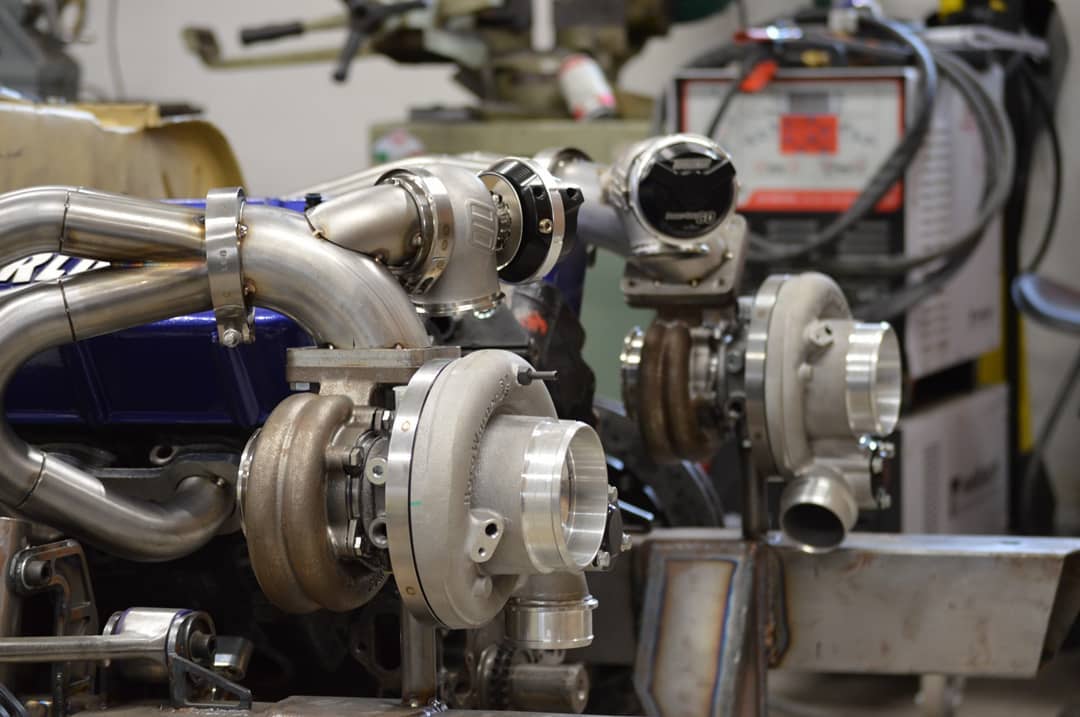
1 ▼
Before assembly
- Clean the air filter box if there is one
- Clean or replace the air filter
- Check intake ducts/piping for leaks
- Is the oil supply line old? Replace this one. It is not possible to clean.
- Clean crankcase ventilation and check/upgrade this for free flow
- Change engine oil and oil filter
2 ▼
Mounting
- A new / used turbo must constantly be lubricated with oil to have an oil film immediately on start-up.
- If a journal-bearing turbocharger is installed, ensure it is connected with full oil pressure from the engine's main oil channel.
- If a ball-bearing turbo is fitted - make sure an oil restrictor is fitted
- Use new steel gaskets - not gaskets on tube / liquid gasket
- Do not use thread tape on the oil inlet adapter
- Drip oil into the turbo oil inlet before start-up
3 ▼
Start-up
- Build up oil pressure before starting the engine
- Check for leaks at idle
- Make sure the engine is adapted for this turbo
- Setup / Tuning may need to be done
4 ▼
Troubleshooting
No / insufficient boost pressure
- Air leakage
- Open / loose wastegate
- Wastegate control does not work
- Vacuum leak
Excess exhaust smoke
- Too much oil in the turbo core due to different reasons
- Too much oil in the engine (the engine is trying to evacuate oil)
- Too high oil pressure / turbocharger cannot evacuate the oil fast enough
- Poor oil evacuation / small oil drain bore
- Poor crankcase ventilation / high crankcase pressure
- Not enough angle on the oil drain piping
Oil in pressure pipes
- Too much oil in the turbo core due to different reasons
- Too much oil in the engine (the engine is trying to get oil out)
- Too high oil pressure / turbocharger cannot evacuate the oil fast enough
- Poor oil evacuation / small oil drain bore
- Poor crankcase ventilation / high crankcase pressure
- Not enough angle on the oil drain piping
Oil in the pressure pipes or exhaust pipes is by far the most common problem. Several reasons can cause oil to build up in the turbo core. It then gets pushed out into the exhaust system and/or pressure pipes.
Example
Problem:
To high oil pressure in combination with bad oil evacuation can cause excess exhaust smoke and oil in pressure pipes
Solution:
Lower the oil pressure a bit AND improve the oil drain. Fixing only one part will not solve the problem.
5 ▼
Common causes of turbo failure
Back pressure
When exhaust back pressure approaches or becomes greater than the boost pressure the turbocharger axle gets an uneven load and can be damaged. . This uneven load makes lubrication difficult and can result in turbo bearing failure. If the back pressure exceeds the charge pressure, the turbo will wear prematurely and in the worst case, break.
Crankcase pressure
High crankcase pressure is common on tuned engines. This high crankcase pressure opposes the turbo's return flow of oil back to the engine. The oil return flow back to the engine with no pressure and therefore it must be a free flow without crankcase pressure opposing the return flow.
If you have high crankcase pressure, the oil cannot evacuate the turbo the right way through the oil return, but is then pushed out through gaskets and ends up in pressure pipes, inlet pipes, and out into the exhaust housing, resulting in all of these cases with extra exhaust smoke. Also called blue smoke and oil smoke as the oil eventually finds its way through the engine.
Oil return size
As already mentioned above, the turbo's oil return does not work under pressure and must have a free flow to the engine. Therefore, it is important to have a properly dimensioned oil return as the oil can freely flow back to the engine. In the case of a journal-bearing turbocharger, this is extra important as there are large amounts of oil that must be evacuated. This is also important with ball-bearing turbos, but then you don't need to have as large return line.
Failed dimensioning of the oil return produces the same consequential error as with too high crankcase pressure.
Oil return slope
Too little inclination of the oil return causes the same problems as with high crankcase pressure and too small oil return piping as the oil cannot flow back to the engine effectively enough.
Oil supply sizing
Journal bearing turbo
A journal bearing turbo must have an oil supply from the engine's main line as it needs to have full oil pressure. This can be compared to the engine crankshaft and main bearings which also need full oil pressure to maintain an oil film to moving parts.
Ball bearing turbo
A ball-bearing turbocharger should not work under pressure. It should only be supplied smaller amount of oil so that it is lubricated. It should not have oil pressure. That's why an oil restrictor is mounted on a ball-bearing turbo.
A ball-bearing turbo fed with oil pressure will have the same problem as with high crankcase pressure and to small oil return.
Oil inlet debris
There are various reasons for turbo (and engine) failure because of debris in the engine oil.
One - you have thread tape on your NPT thread on the oil feed so the thread tape follow the oil into the turbocharger bearings.
Two – The turbo core is much more sensitive than the heavy duty bearings in the engine. The turbo is very precise and minor deviations can cause problems.
Three - When making and mounting the oil supply hose. Debris can follow and end up in the turbo charger
Debris in the engine oil causes damage to the turbo bearings and the engine bearings.
NOTE. Lighter debris does not damage engine bearings as much as turbo bearings. But lighter debris leading to turbo failure can also cause the engine bearings to fail.
Oil pressure
An oil pressure that is too low causes a journal bearing turbo to break quite immediately as it needs proper oil pressure. This also applies to a ball-bearing turbo, but it should not have pressure, -only drops that keep the bearing lubricated. Regardless of which turbo you have, you must ensure correct oil pressure and then adjust this if you have a ball-bearing turbo. Another aspect is engines that have oil pressure higher than "normal". Then the turbo can push oil into the turbo and or compressor housing.
Inlet air debris
It is often difficult to keep things completely clean when assembling car parts, and in this case, turbo units and inlets. However, it is absolutely necessary as debris that enters the inlet pipe when the turbo is spinning can cause major damage to compressor wheels with consequential errors such as imbalance and oil leakage. This sometimes leads to turbo failure.
Over-revving
The turbo is simply over-revved so both the turbine blades and the bearing part are damaged.
When the turbo journal bearings are empty of oil, a larger radial play is experienced.